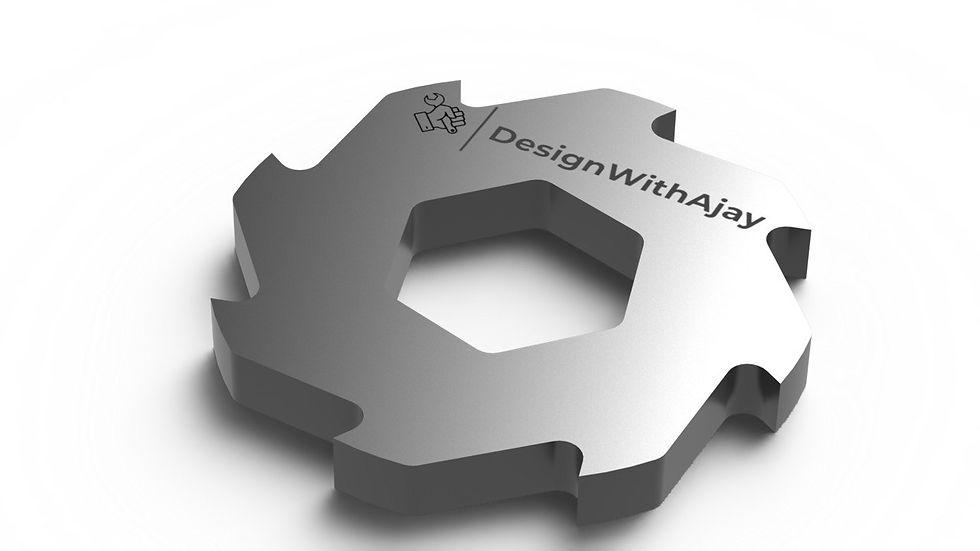
Industrial shredder machines are indispensable in various sectors, from recycling plants to manufacturing facilities, for efficiently processing materials into smaller fragments. The performance and longevity of these machines heavily rely on the quality and resilience of their blades. Choosing the appropriate blade material is crucial to ensure optimal shredding efficiency and durability. In this comprehensive blog post, we will delve into the realm of industrial shredder machine blade materials, examining the advantages and disadvantages of various options to aid you in making well-informed decisions when selecting blades for your shredder.
Understanding Industrial Shredder Machine Blade Materials:
Blades used in industrial shredder machines endure extreme forces and wear during operation. Therefore, selecting the right blade material is paramount to withstand these demands and maintain optimal performance. Let's delve into some common blade materials used in industrial shredder machines and their respective pros and cons:
1. High-Speed Steel (HSS):
Pros:
High hardness and wear resistance, suitable for shredding tough materials such as metals and plastics.
Excellent edge retention, reducing the need for frequent sharpening or replacements.
Can withstand high temperatures generated during shredding operations.
Cons:
Relatively higher cost compared to some other blade materials.
Prone to corrosion if not properly maintained, requiring regular cleaning and lubrication.
2. Tool Steel:
Pros:
Exceptional toughness and impact resistance, making tool steel blades ideal for shredding heavy-duty materials.
Good wear resistance, ensuring prolonged blade life even when shredding abrasive materials.
Customizable through heat treatment for enhanced hardness and durability.
Cons:
Requires regular maintenance to prevent corrosion and ensure optimal performance.
Higher initial cost compared to some other blade materials.
3. Carbide:
Pros:
Exceptional hardness and wear resistance, resulting in highly durable and long-lasting blades.
Maintains sharpness for extended periods, reducing the frequency of blade replacements.
Ideal for shredding abrasive and high-density materials with minimal wear.
Cons:
Higher initial cost compared to steel-based blade materials.
Brittle nature makes carbide blades susceptible to chipping or breakage if subjected to excessive impact or shock.
4. Alloy Steel:
Pros:
Offers a balance of hardness, toughness, and wear resistance, making alloy steel blades versatile and durable.
Cost-effective option compared to high-performance blade materials.
Can be tailored through alloying for specific shredding applications.
Cons:
May require more frequent sharpening or replacement compared to carbide blades when shredding abrasive materials.
Susceptible to corrosion if not properly maintained.
5. Bi-Metal:
Pros:
Combines the toughness of steel with the wear resistance of carbide, resulting in blades with enhanced durability and performance.
Ideal for shredding a wide range of materials, including metals, plastics, and wood.
Offers a cost-effective alternative to solid carbide blades.
Cons:
Higher initial cost compared to traditional steel blades.
Limited availability of specialized bi-metal blades for specific shredding applications.
Conclusion:
Selecting the appropriate blade material is critical for optimizing the performance and longevity of industrial shredder machines. By understanding the advantages and disadvantages of different blade materials, you can make informed decisions tailored to your specific shredding requirements. Consider factors such as the types of materials to be shredded, operational conditions, maintenance needs, and budget constraints when choosing the most suitable blade material for your industrial shredder machine. Investing in high-quality blades crafted from durable materials will not only enhance shredding efficiency but also minimize downtime and maintenance costs in the long run, ensuring continuous and reliable operation of your shredding equipment.
Comments