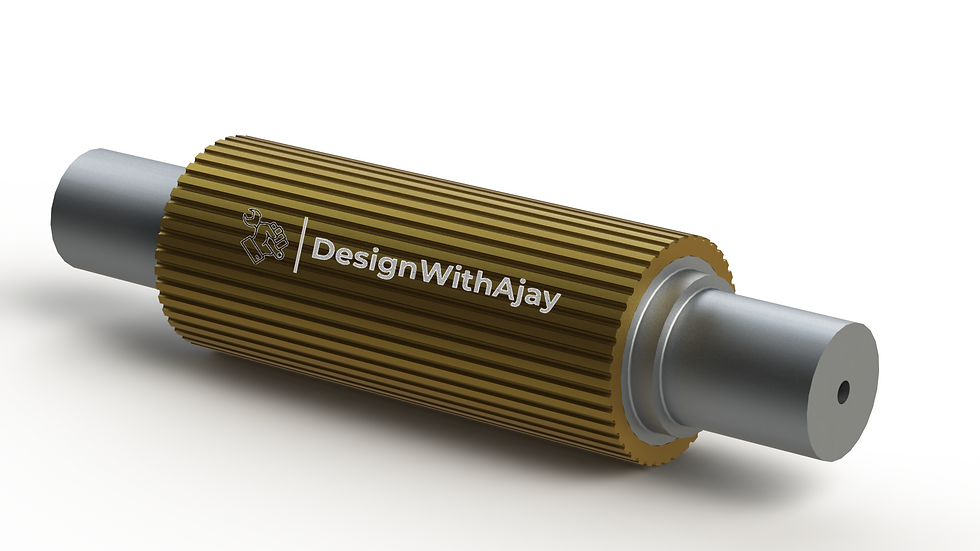
In the world of manufacturing and industrial processing, rubber roller shafts play a vital role in facilitating smooth and efficient material handling, coating, and processing operations. From printing and packaging to textiles and converting, rubber roller shafts provide reliable support and rotation for a variety of rubber rollers used in diverse applications. In this comprehensive guide, we'll explore what rubber roller shafts are, their construction, applications, advantages, and considerations for optimal usage.
Understanding Rubber Roller Shafts:
Rubber roller shafts are cylindrical shafts or cores made from metal or composite materials that support and rotate rubber rollers in various industrial processes. These shafts serve as the central axis around which the rubber roller is mounted, providing stability, alignment, and rotational motion. Rubber roller shafts are commonly used in applications such as web handling, printing, laminating, embossing, and material conveying.
Construction of Rubber Roller Shafts:
Rubber roller shafts are typically constructed from materials such as steel, stainless steel, aluminum, or composite materials like carbon fiber or fiberglass. The shafts may be solid or hollow, depending on the specific application requirements and load-bearing capacity. They are precision-machined to tight tolerances to ensure concentricity, straightness, and dimensional accuracy.
The surface of rubber roller shafts may be treated or coated with materials such as chrome, ceramic, or rubber to enhance wear resistance, reduce friction, and improve traction with the rubber roller. Additionally, rubber roller shafts may feature keyways, splines, or other drive mechanisms to transmit rotational motion from a motor or drive system to the rubber roller.
Applications of Rubber Roller Shafts:
Rubber roller shafts find application in a wide range of industries and processes, including:
Printing and Converting: In the printing and converting industry, rubber roller shafts are used in printing presses, laminators, slitters, and coating machines to support and rotate rubber rollers for applying ink, adhesives, coatings, and finishes to various substrates such as paper, film, and textiles.
Packaging and Labeling: Rubber roller shafts are employed in packaging machinery for feeding, sealing, and labeling operations. They provide reliable support and rotation for rubber rollers used in processes such as bagging, wrapping, sealing, and palletizing.
Textile and Nonwoven Manufacturing: In textile and nonwoven manufacturing processes, rubber roller shafts are used in calenders, embossing machines, and laminators for fabricating, finishing, and bonding textile materials. They ensure uniform pressure and tension across the width of the fabric for consistent quality and performance.
Material Handling and Conveying: Rubber roller shafts are utilized in material handling equipment such as conveyor systems, feeders, and rollers for transporting, aligning, and processing materials in manufacturing, warehousing, and distribution operations.
Advantages of Rubber Roller Shafts:
1. Precision Engineering: Rubber roller shafts are manufactured to precise tolerances, ensuring concentricity, straightness, and dimensional accuracy for reliable performance and alignment with the rubber roller.
2. Durability and Wear Resistance: Rubber roller shafts are constructed from durable materials and coatings to withstand the rigors of industrial processing, including abrasion, corrosion, and chemical exposure.
3. Smooth Operation: Rubber roller shafts provide smooth and consistent rotation of rubber rollers, minimizing vibration, chatter, and surface imperfections in processed materials.
4. Customization Options: Rubber roller shafts can be customized to meet specific application requirements, including shaft diameter, length, surface finish, and drive configurations.
5. Compatibility: Rubber roller shafts are compatible with a wide range of rubber rollers, including various durometers, surface finishes, and coverings, making them suitable for diverse industrial applications.
Considerations for Optimal Usage:
To maximize the performance and longevity of rubber roller shafts, consider the following factors:
Shaft Material: Select a shaft material and coating that is compatible with the operating environment and processing conditions, including temperature, humidity, chemical exposure, and abrasion resistance.
Shaft Alignment: Ensure proper alignment of the rubber roller shaft with other machine components, including bearings, guides, and drives, to prevent excessive wear, vibration, and misalignment.
Maintenance: Implement a regular maintenance program for inspecting, cleaning, and lubricating rubber roller shafts to prevent corrosion, contamination, and premature wear. Replace worn or damaged shafts and bearings promptly to avoid production downtime and quality issues.
Load Capacity: Consider the load-bearing capacity of the rubber roller shaft in relation to the weight, size, and tension of the rubber roller and processed materials. Choose shafts with sufficient strength and stiffness to support the intended load without deformation or deflection.
Safety Precautions: Adhere to safety protocols and guidelines when installing, operating, and servicing rubber roller shafts, including proper machine guarding, lockout/tagout procedures, and personal protective equipment (PPE) for maintenance personnel.
Conclusion:
Rubber roller shafts are essential components in a wide range of industrial processes, providing reliable support and rotation for rubber rollers used in printing, converting, packaging, textile manufacturing, and material handling applications. With their precision engineering, durability, and customization options, rubber roller shafts contribute to efficient and consistent material processing, ensuring high-quality results and productivity. By understanding their construction, applications, advantages, and considerations for optimal usage, businesses and industries can leverage rubber roller shafts to enhance the performance and reliability of their equipment and processes.
Comments