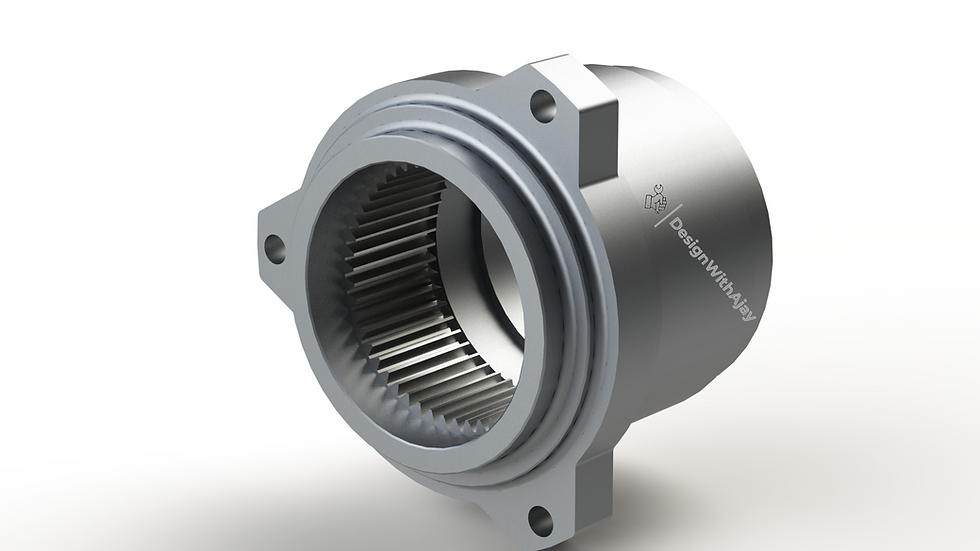
Internal gear flanges are a critical component in various mechanical systems, playing a pivotal role in transmitting power and motion efficiently. This guide aims to explore the intricacies of internal gear flanges, their design principles, applications, and the benefits they offer.
1. Introduction to Internal Gear Flanges
Internal gear flanges belong to the broader category of gears, which are mechanical devices used to transmit rotational motion and power from one part of a machine to another. Unlike external gears, where the teeth are located on the outer circumference of the gear, internal gear flanges feature teeth on the inner circumference. This design allows them to mesh with external gears, providing a mechanism for torque transmission and motion transfer.
2. Design Principles
The design of internal gear flanges involves careful consideration of various factors, including tooth profile, pitch diameter, pressure angle, and module (or diametral pitch in the imperial system). These parameters determine the performance characteristics, strength, and efficiency of the gear system.
Tooth Profile: Internal gear flanges typically feature involute tooth profiles, which ensure smooth engagement and minimal backlash during operation.
Pitch Diameter: The pitch diameter is a crucial parameter that determines the gear's size and compatibility with other gears in the system.
Pressure Angle: The pressure angle influences the contact pattern and load distribution between mating gears. Common pressure angles include 14.5°, 20°, and 25°.
Module: In metric systems, module refers to the ratio of the pitch diameter to the number of teeth. In the imperial system, diametral pitch is used, which represents the number of teeth per inch of pitch diameter.
3. Applications of Internal Gear Flanges
Internal gear flanges find applications across various industries and machinery, including:
Gearboxes and Transmissions: Internal gear flanges are commonly used in automotive transmissions, industrial gearboxes, and power transmission systems to transfer torque and motion between rotating shafts.
Rotary Actuators: These components are integral to rotary actuators used in robotics, manufacturing automation, and machinery control systems.
Wind Turbines: Internal gear flanges are employed in the gearbox of wind turbines to increase the rotational speed of the rotor and generate electricity efficiently.
Heavy Machinery: In heavy machinery such as construction equipment, internal gear flanges play a vital role in transmitting power to drive wheels, tracks, and hydraulic systems.
4. Benefits of Internal Gear Flanges
Compact Design: Internal gear flanges offer a compact solution for power transmission, making them ideal for applications where space is limited.
High Torque Transmission: Due to their tooth geometry and engagement, internal gear flanges are capable of transmitting high levels of torque efficiently.
Smooth Operation: Properly designed internal gear flanges provide smooth and quiet operation, reducing vibrations and wear in the system.
Versatility: Internal gear flanges can be customized to meet specific application requirements, including different tooth profiles, materials, and heat treatment processes.
5. Conclusion
Internal gear flanges are indispensable components in various mechanical systems, offering efficient torque transmission, compact design, and smooth operation. Understanding the design principles and applications of internal gear flanges is essential for engineers and designers involved in the development of machinery and equipment across industries.
In conclusion, internal gear flanges represent a cornerstone of modern mechanical engineering, providing reliable and efficient solutions for power transmission and motion control.
留言